Laser Micromachining Technology
The Hi-Nano team boasts over two decades of focused development in laser micromachining technologies, enabling industry advancement. Our expertise shines in solving intricate micron-level challenges, particularly with ultra-hard materials like diamonds, sapphire, silicon carbide , lithium niobate, optical glass and beyond. Whether it's tailored machining or cutting-edge system production, rely on Hi-Nano for unmatched proficiency. Join us in this journey now!
Features:
- Achieve micron-level precision with utmost accuracy.
- Employ a non-contact process to ensure minimal particle formation and maintain cleanliness.
- Experience negligible heat-affected zone (HAZ) for pristine results.
- Minimize chipping and micro cracks during the cutting process.
Applications:
- Optical wafer dicing for precise manufacturing in the optics industry.
- Cutting AR and VR glasses with utmost precision.
- MEMS wafer dicing for micro-electromechanical systems.
- Cutting coated lenses with exceptional accuracy.
- Laminated optics cutting for seamless integration of optical components.
- Optical sensor cutting for intricate sensor devices.
Features:
- Capable of cutting both straight lines and free shapes with precision.
- Accommodates a wide range of glass thicknesses, from ultra-thin and bendable to ultra-thick glass.
- Enables cutting and drilling of various optical glass types with exceptional accuracy.
- Delivers high cutting quality for coated lenses, ensuring superior results.
Applications:
- Cover glass and view windows for electronic devices and displays.
- Optical sensors, providing accurate and reliable sensing capabilities.
- Glass substrates for diverse electronic and optical applications.
- Car mirrors, ensuring safety and clarity for drivers.
- Optical lenses, crafting lenses with precision and efficiency.
- Glass components for various industrial and consumer products.
- Laminated glass for enhanced durability and functionality in specialized applications.
Features:
- Holes available in straight or hourglass shapes.
- High aspect ratio capabilities, extending up to 1:20.
- Achievable minimum micro hole size, with diameters as small as 20 micrometers.
- Remarkable precision levels for consistent results.
- Cost-effective manufacturing process.
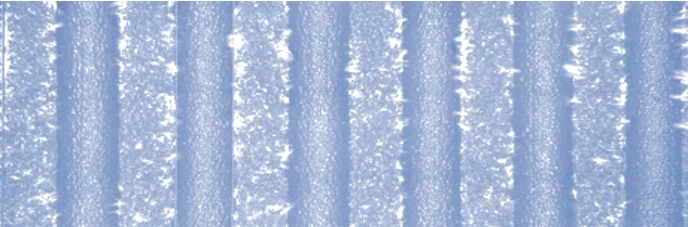
Applications:
- Miniaturized cameras and sensors for smartphones and wearables.
- Endoscopes and minimally invasive medical devices for internal imaging and diagnostics.
- Micro optics for coupling light signals in compact optical communication devices.
- Miniature Lidar systems for robotics, drones, and autonomous vehicles.
- Optical sensors for fingerprint recognition and gesture control.
- Compact vision systems.
- Smart glasses and AR devices.
- Mini. cameras and sensors for (UAVs) and drones.
Applications:
- Employed as wafer chucks, susceptors, and carriers in the Chemical Vapor Deposition (CVD) and epitaxy processes for semiconductor fabrication equipment.
- Utilized as electrodes and components within dry etching equipment’s chambers and more.
- Integrated into aircraft brake disks to enhance performance.
- Utilized for mechanical components across diverse industries, underscoring its exceptional qualities of high temperature resistance, hardness, and lightweight characteristics.
Features:
- High Precision
- Minimal Material Loss
- Reduced Heat Affected Zone
- Processing of Complex Shapes
- Versatility
- Minimal Contamination
- High Throughput
- Easy Automation
- No Tool Wear
- Environmental Friendliness: No need for coolants or lubricants.
Applications:
- Power Electronics: SiC is extensively used in power semiconductor devices.
- High-power laser diodes: used in communication and industrial processes.
- High Frequency Wireless Communication Devices.
- Aerospace and Defense
- Automotive: SiC-based inverters, diodes, MOSFETs, and IGBTs.
- Industrial Heating
- Seals and Bearings